[CGT CDMO의 이해③]
프로세스 확장: 임상적 요구 예측
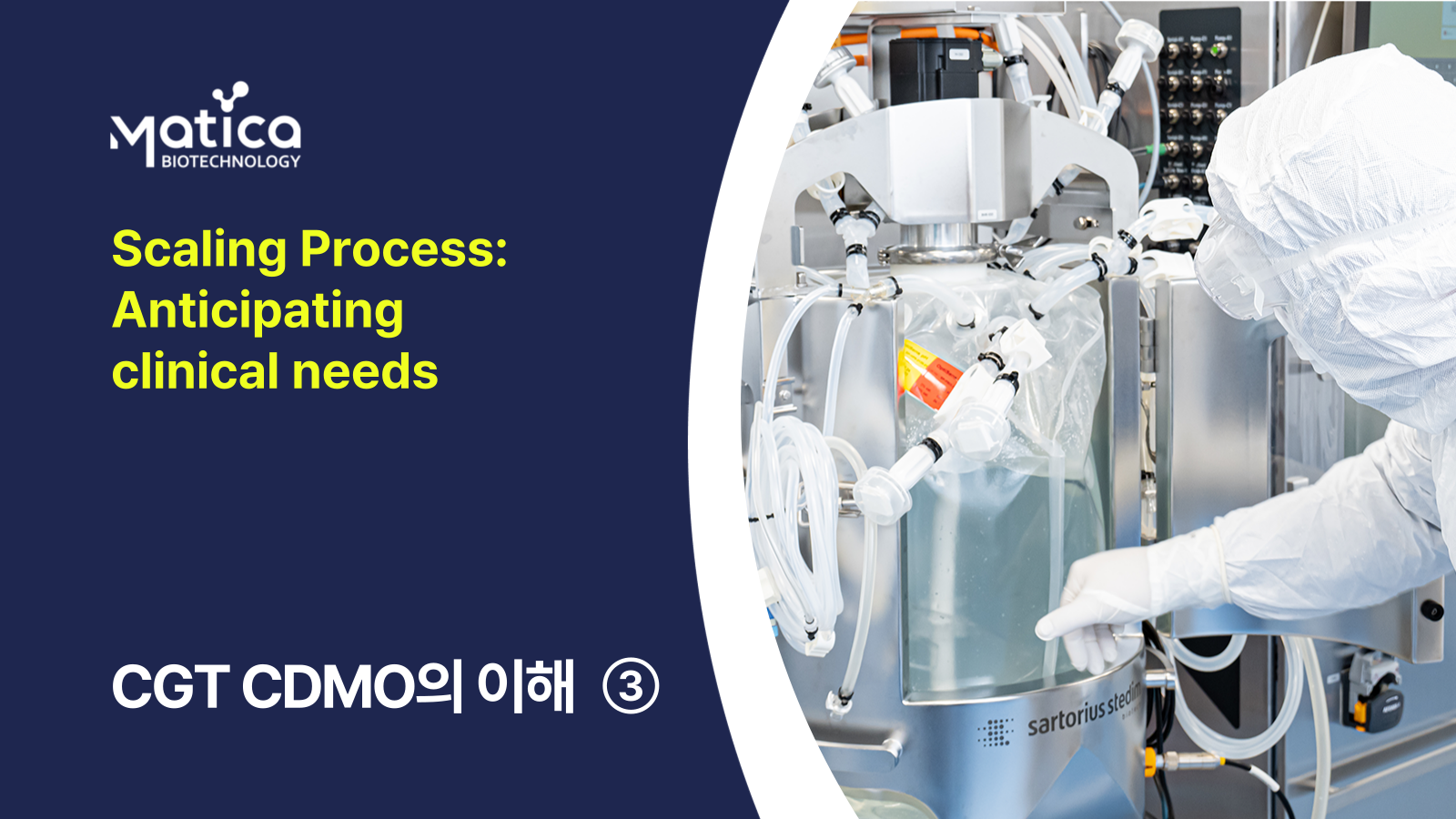
미국 텍사스에 있는 CGT CDMO 전문기업 마티카 바이오테크놀로지(이하 마티카 바이오)가 공개한 백서(White Paper)를 기반으로 세포∙유전자치료제 CDMO의 구조와 기능을 알아보는 [CGT CDMO의 이해] 칼럼을 8편 연재합니다.
3편에서는 세포∙유전자치료제 개발하는 과정에서 바이럴 벡터(Viral Vector)를 생산하기 위해 어떤 제조 플랫폼을 선택해야 하는지 알아보겠습니다.
세포∙유전자치료제를 개발하는 초기 단계에는 소량의 바이럴 벡터만으로도 충분하다. 하지만 개발 단계가 진전되고 상업화 단계에 가까워질수록 많은 양의 바이럴 벡터가 필요하게 된다.
이때 효율적으로 생산량을 늘리기 위해 장비와 시설에 투자해야 할뿐만 아니라 바이럴 벡터 제조 프로세스에도 변화를 줘야 한다.
공정효율화를 위한 고려사항(Retrofitting Consideration)
바이럴 벡터 생산량을 늘리기 위해서는 제조 프로세스를 조정하고 최적화 해야 한다.
먼저 바이럴 벡터 제조에 영향을 미치는 배양배지, 세포 배양 조건, 성장인자 등 다양한 조건들을 최적화한다.
다음으로 바이럴 벡터 제조 프로세스 단계마다 품질을 확인하고, 관리할 수 있는 모니터링 시스템을 갖춰야 한다. 고품질의 바이럴 벡터를 사용해 개발한 세포∙유전자치료제를 환자에게 투여했을 때 부작용이 발생할 가능성이 적다. 또 동일한 바이럴 벡터를 활용해 더 많은 양의 세포∙유전자치료제를 만들 수 있다.
2편에서 언급한 것처럼 어떤 바이럴 벡터를 선택하는지에 따라 유전자치료 프로토콜이 달라진다. 함께 사용할 수 있는 세포도 달라진다. 선택한 바이럴 벡터의 특성을 고려해 어떤 숙주세포를 사용할 것인지, 제조공정은 어떻게 할 것인지 결정해야 한다.
제조 시간을 단축하는 것도 제조 효율을 높일 수 있는 방법의 하나다. 싱글유즈시스템(Single use system)과 완전 폐쇄형 제조시스템을 사용하면 무균 상태를 유지해 오염 위험을 최소화하고 작업자 안전과 제품 무결성을 보장할 수 있다. 특히 제조 프로세스 자동화로 생산 시간을 단축하고 효율성을 높일 수 있다.
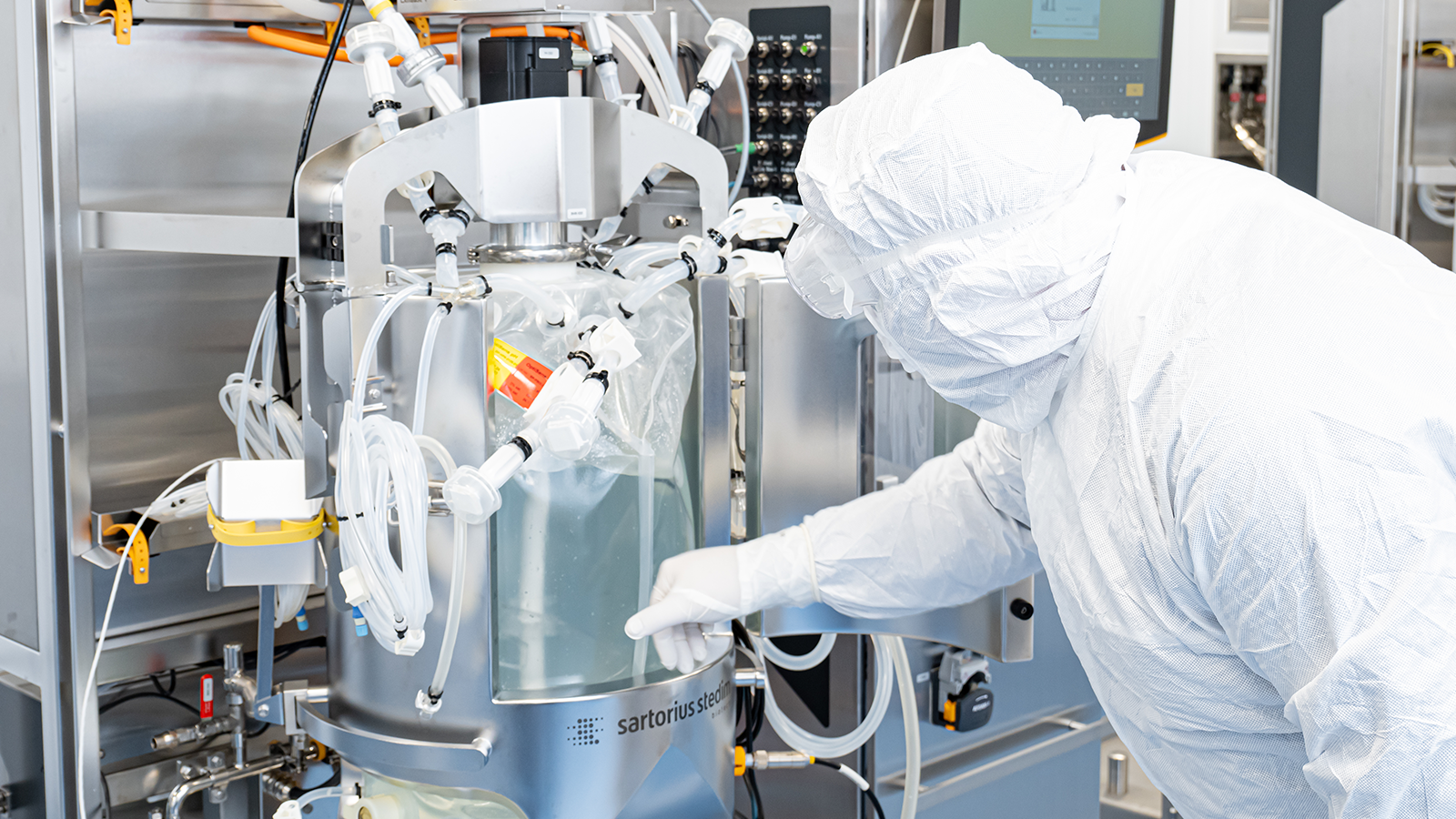
<세포 플랫폼을 만들고 있는 마티카바이오 직원>
프로세스 비교(Process Comparisons)
바이럴 벡터를 제조할 때 아래 3가지 제조 플랫폼이 주로 사용된다. 세포의 성장을 촉진하고 최상의 품질로 바이럴 벡터를 제조할 수 있는 방법이다. 생산량과 효율을 높이기 위해서 플랫폼을 전환해야 할 수도 있다.
1. 부착성세포 증식 플랫폼 (Adherent Cell Proliferation Platforms)
플랫폼 구축 및 유지·보수에 비용이 적게 든다. 플라스크(Flask)에서 단층세포 배양을 할 수 있고, 고정층 세포배양기(The fixed bed bioreactors)를 활용해 생산량을 늘릴 수 있다.
고정층 세포배양기를 사용하면 여러가지 입출력 매개 변수를 실시간으로 모니터링 할 수 있다.
하지만 평평한 표면에서 세포가 성장해 신체 장기와 비교했을 때 세포 형태, 유전자 발현, 신호 전달 경로 등이 다를 수 있다. 치료제로 개발했을 때 효능에 한계가 있을 수 있다.
2. 부유세포 증식 플랫폼 (Suspension Cell Proliferation Platforms)
부착성세포 증식 플랫폼보다 비용이 많이 들지만 세포의 생리학적 상태를 잘 반영해 최종적으로 높은 품질의 치료제를 개발할 수 있다.
특히 부착성세포 증식 플랫폼 보다 무혈청 성장을 보다 유지할 수 있다는 장점이 있다. 혈액에서 추출한 혈청에는 세포 배양시 가변성과 잠재적인 면역 반응을 유발할 수 있는 다양한 성장 인자와 단백질이 포함되어 있다. 성장 배지에서 혈청을 제거함으로써 통제된 환경에서 세포를 성장시킬 수 있다. 이렇게 만들어진 치료제는 환자의 치료 중 면역반응을 일으킬 위험을 줄일 수 있다.
부유세포 증식 플랫폼은 생산용량에 제한이 없지만, 임상단계에 따라 50 L, 200L, 500 L 등 다양한 용량의 세포배양기(bioreactor)가 사용된다.
3. 마이크로캐리어 하이브리드 세포 배양 플랫폼 (Microcarrier Hybrid Systems)
부착성세포 증식 플랫폼과 부유세포 증식 플랫폼의 장점이 혼합되어 있다. 세포는 액체 매질에 부유하는 마이크로캐리어(microcarrier)라고 불리는 작은 고체입자 위에서 성장한다.
마이크로캐리어를 활용해 부착성세포 배양도 가능할 뿐만 아니라, 부유세포 증식 플랫폼 보다 세포 밀도가 높아 생산성과 효율성이 높다.
플랫폼 고려 사항(Platform Considerations)
안정적인 용량(Reliable Capacity)
임상시험 및 상업화로 인해 더 많은 바이럴 벡터를 생산할 필요가 있을 때 제조 플랫폼 변경을 생각할 수 있다.
10~15L 정도의 소량이 필요한 경우 부착성세포 증식 플랫폼을 이용해 플라스크 단층세포 배양, 고정층 세포배양기 또는 이들의 조합을 이용하는 것이 좋다.
50 L 이상이 필요한 경우 부유세포 증식 플랫폼으로 전환하면 제조공정을 단순화 하고, 배양 시간을 단축해 전체 비용을 절감할 수 있다.
기술 및 전문성(Technology and Expertise)
개발 초기단계에서는 부착성세포 증식 플랫폼이 효과적일 수 있다.
부착성세포 증식 플랫폼은 부유세포 증식 플랫폼에 비해 공정이 간단하고 제어해야 할 변수가 훨씬 적다. 독성 연구, 효능 입증을 위해서는 소량만 생산해도 되기 때문이다.
세포주를 서스펜션 플랫폼에 적응시키기(Acclimating Cell Lines to Suspension Platforms)
부착성세포 증식 플랫폼, 부유세포 증식 플랫폼, 마이크로캐리어 하이브리드 세포 배양 플랫폼은 각각 세포의 성장 조건이 동일하지 않다. 어떤 플랫품을 선택하는지가 바이러스 형질감염 또는 바이러스 감염단계에 영향을 미칠 수 있다. 최종적으로 치료제의 품질과 특성에도 영향을 줄 수 있다.
부착성세포 증식 플랫폼의 단점을 보완하기 위해 부유세포 증식 플랫폼으로 전환해아 하는 경우가 자주 있다. 이때 치료 안전성과 효능이 영향을 받지 않도록 세심하게 주의 해야 한다.
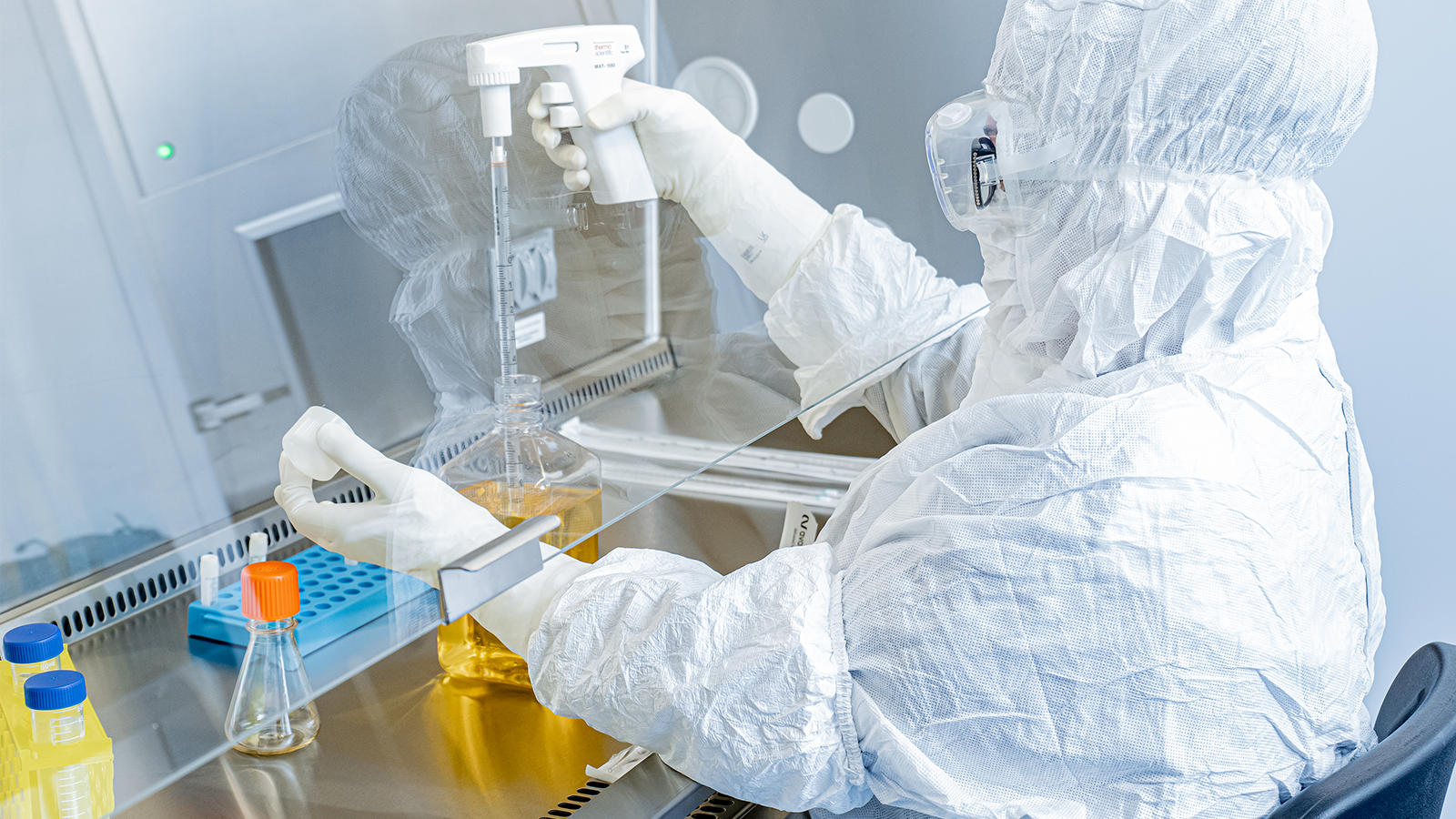
<플랫폼 안정화 실험중인 마티카바이오 직원>
마티카 바이오는 수 많은 스크리닝 실험을 거쳐 대규모 부유세포 증식 플랫폼의 여러가지 설정을 자동으로 반영하는 시스템을 갖추고 있다. 배양시설이 들어갈 공간 정보를 적용해 부착성세포 증식 플랫폼에서 부유세포 증식 플랫폼으로 효과적으로 전환할 수 있도록 지원한다. 다운스트림 정제 프로세스를 최적화하고 생산량 증대를 위한 공정(Upstream Process)으로 전환할 때도 제품 품질에 부정적인 영향을 미치지 않도록 운영하고 있다.
처리 시간(Processing Times)
부착성세포 증식 플랫폼으로 원하는 용량을 배양할 수 있다면 플랫폼 전환을 하지 않아도 된다. 하지만 개발 단계가 진전되고 상업화 단계로 갈수록 더 많은 양의 바이럴 벡터가 필요하게 되고, 제조 플랫폼을 변경해야 할 수도 있다.
부유세포 증식 플랫폼이나 마이크로캐리어 하이브리드 세포 배양 플랫폼으로 전환할 경우 일반적으로 생산기간이 길어진다. 이때 완전 폐쇄형 시스템(Fully Closed System)과 싱글유즈시스템(Single Use System)을 도입하면, 세척, 멸균 등 프로세스를 줄일 수 있다. 공정 내 분석 및 모니터링을 구현해 샘플링 작업을 최소화해 생산 시간을 단축할 수 있다. #
